8 tried and tested techniques for decreasing dust emissions in quarries
From collective to personal protection equipment and the implementation of appropriate procedures, find out a number of quarry-tested solutions.
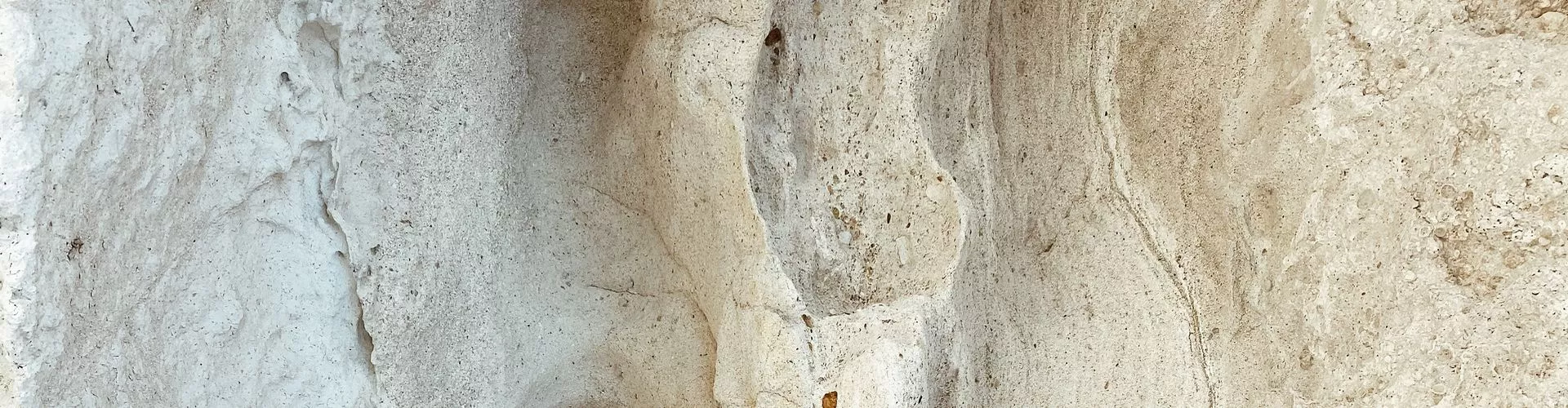
Quarry dust is a health hazard that after long-term inhalation is known to cause silicosis, an irreversible lung disease. It also has an impact on the environment, with dust fall-out polluting and contaminating the soil. Preventing dust emissions is therefore an unavoidable issue, on which there is a guide published by France’s National aggregate producers’ union (UNPG). Their recently updated guide runs through a number of quarry-tested solutions, from collective to personal protection equipment and the implementation of appropriate procedures.
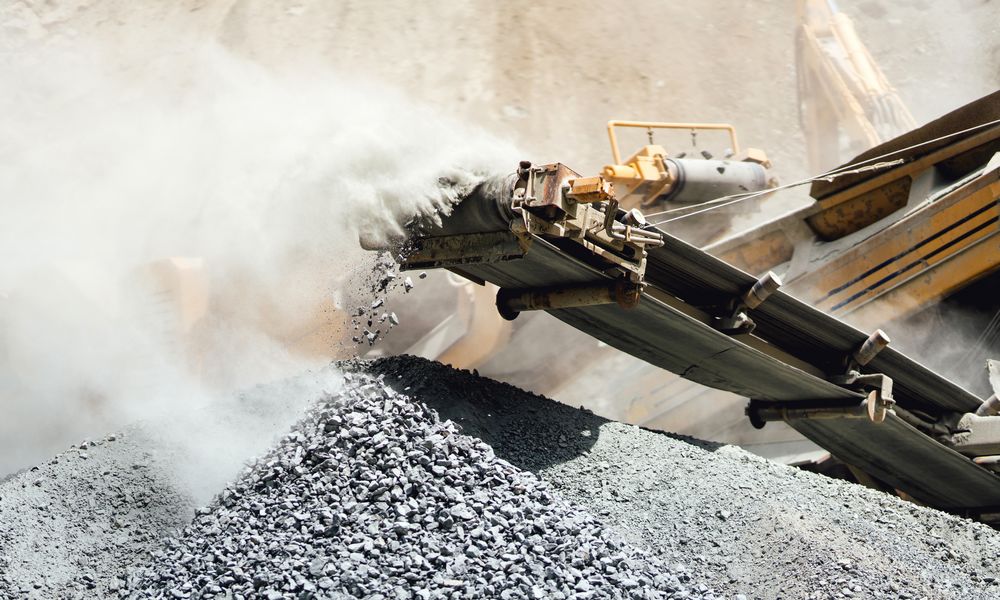
Download the UNPG guide (French only)
1. Enclosure installations
Enclosure of equipment where possible is the first line of attack. It’s a viable option for screens, by installing metal or flexible covers fitted with dust-tight seals. The UNPG also advocates polyurethane and rubber tiling, whose abrasion resistance beats that of metal grilles while saving on maintenance downtime, lasting longer, and decreasing noise.
Special attention must also be paid to the dust-tightness of conveyers, stockpilers, and chutes.
2. Dust extraction by suction
Several types of suction systems exist that can be installed to limit the occupational hazard caused by dust:
- Central suction
- As-required suction
- Electrostatic dust collection, which ionizes particles in suspension and attracts them toward a metal shroud
- Vacuum cleaning during cleaning campaigns:
- mobile vacuuming with a suction truck or excavator
- fixed central vacuuming comprising a suction unit, a suction nozzle, and a vacuum cleaner.
In certain cases, the extracted dust can be reintegrated with the aggregate.
3. Dust suppression
This involves using water to settle dust clouds. It can be sprayed, atomized (low pressure), or nebulized (high pressure). The UNPG draws attention to the need to use tensioactive agents, to carefully match the spray nozzle size to that of the emitted dust particles, and to the importance of containing the volume to enable optimum processing.
The access tracks also need to be sprayed (fixed, mobile, or vehicle-mounted systems).
4. Maintenance and upkeep of installations
The UNPG puts forward several approaches for limiting the personnel’s exposure to dust emissions. This involves deliberation on the design of the installations (e.g., choosing easy-clean surfaces), on the safety procedures to be implemented, and on the organization of maintenance and cleaning operations, for example,
- avoid always using the same personnel for the same cleaning task
- define a maximum weekly time to be spent on cleaning
- take maximum steps to avoid operator presence in the screen enclosure
- etc.
5. Automation and video control
Make way for new technologies! With remote control and real time monitoring, operators are isolated from dust emissions as well as from noise and vibrations. Using a programmable logic controller, a computer, or a combination of both along with sensors (jamming sensors, rotation detectors, etc.), you can make it so no one needs to work on the site except for breakdown repairs and inspection visits.
Discover 4 digital technologies for working natural stone
6. Machinery cabs, fixed control booths, ancillary rooms
Dust-free atmospheres are created in rooms supplied with filtered air kept at slightly higher than atmospheric pressure to prevent dust ingress. This technique also concerns fixed control booths, where no material is handled, as well as ancillary rooms such as laboratories.
As far as machinery cabs are concerned, special attention must be paid to their air filtration system, their maintenance, the cleaning conditions, and the cleanness of work attire. Cabs pressurized with purified air are invaluable for decreasing the occupational hazard from dust in a quarry. Old, unequipped machinery can be retrofitted with a complementary ventilation module.
7. Breathing protection
When operators cannot be totally isolated from dust, it’s time for PPE to take over. Breathing protection devices range from the simple half-face dust mask to the ventilated full-face mask with filter and independent air source.
The UNPG has conducted a fitness test on these various devices in order to measure the concentration of particles inside and outside the mask. It turns out that the protection offered by the disposable half-mask FFP3 is inadequate, unlike the TM3 assisted ventilation appliance. The efficacy of the P3 “asbestos” half-face mask with cartridge filter is deemed satisfactory.
8. Dust measurement by photometry
Photometry is an indispensable diagnosis tool for quarry operators wondering how to assess the dust emission source points in quarries. The presence of dust can be measured to a high degree of accuracy on a wide variety of activities:
- filter blowing
- quartering
- specific maintenance jobs
- surveillance rounds
- etc.
Another interesting measuring method for optimizing stone quarry operation is photogrammetry, which looks at the volumetrics of the quantities extracted or about to be extracted. This article goes into the details!
All the information you need for decreasing dust emissions in your quarry will be on show at Rocalia, the trade show for natural stone professionals. Come and meet manufacturers and suppliers, who can assist you in decreasing occupational hazards!
© Photo credit: Hoda Bogdan / Adobe Stock